The technically trained sales team at Total Filtration Services is uniquely qualified to deliver filtration solutions for both air and liquid applications across a wide variety of industries. Review our library of customer case studies to gain a better understanding of what it’s like to partner with TFS and lower the total cost of ownership for your filtration.

Liquid Cartridge Solution Improves Safety and Provides Cost Savings
TFS addresses a serious safety risk and saves a chemical manufacturer over $300,000 in product and labor costs.

Protecting Equipment with Permatron Prevent Screens
This customer is a tier-1 supplier to the automotive industry located in Michigan. They manufacture automotive interior, exterior and wheel trim and have several facilities with applications requiring filtration.

Developing a Custom Filtration Solution for an Aerospace Customer
TFS' success in delivering significant costs savings to a major aerospace customer as a result of its technical expertise and strong relationships with filter manufacturers

Dust Filtration Solution Saves Candy Manufacturer $30,000
The company involved in this case study is a major candy manufacturer that employs over 500 workers at its 650,000 square foot location in the southern region of the United States.

Improving Air Quality and Protecting Equipment for a Power Transformer Manufacturer
This case study involves one of the largest manufacturers of high voltage power transformers in the world. Their products are used throughout North America by power generation plants and various industrial manufacturing facilities.

Resolving Filter Failure and Preventing Downtime for Data Centers
A privately-owned data center in the Ashburn, VA area was experiencing issues with collapsing filters in their rooftop air handling units and required a new filtration solution to extend filter life and protect cooling coils.

Improving CNC Machine Filtration for International Technology Company
The customer in this case study is an international technology company that designs and manufactures connectivity and sensor products for a variety of industries.

Resolving a Filter Collapse Issue for a Hospital
A major hospital in the Saint Paul, Minnesota area contacted TFS about a significant filter failure issue they were experiencing with several of their air handling units.

Parker PCLAS Successfully Replaces Resin Bond Cartridge for Global Manufacturer
The customer involved in this case is a global advanced materials and specialty additives company that produces a wide range of products found in items people use every day. They manufacturer varnish for various industries.

Resolving a Fouling Issue for a Wind Turbine Manufacturer
The company involved in this case study is a multi-national manufacturer of wind turbines that meets the needs of alternative energy production worldwide.

Improving Cleanroom Filtration for an Appliance Manufacturer
TFS helps a property management company that provides maintenance services for a major appliance manufacturer in the Memphis. The facility employs 530 people who assemble, paint, and ship kitchen appliances

Resolving a Product Quality Issue for a Major Cheese Factory
The company is a large cheese manufacturer located in the South Dakota area that makes cheese, whey, lactose, and anhydrous milk fat products for some of the largest food brands in the world.

Improving Paint Booth Operations for an Automotive Supplier
This tier-one automotive supplier that manufactures vehicle interior, exterior, and wheel trim. After years of purchasing their filters from a local MRO supplier, they began partnering with TFS to improve their filtration.

Achieving Significant Cost Savings at an Automotive Assembly Plant
Extensive experience in paint booth management allowed TFS field experts to provide technical support and improve the performance of paint booth operations at a large automotive assembly plant.

Liquid Filter Bag Solution Saves Global Textile Manufacturer $100,000
TFS worked with process engineers from a global textile manufacturer to address concerns with failing liquid bag filters and to identify potential cost savings.

Resolving a Liquid Bag Filter Issue for Food Processing Plant
This customer is a large food manufacturer in SW Minnesota. The food processing plant involved in this cases study makes a variety of cheese products, such as single slices of American cheese.

Engineering a Liquid Cartridge Solution for a Petroleum Refinery
A sophisticated crude oil processing company, called upon TFS to identify a replacement for the liquid cartridges used to filter crude oil being unloaded from railcar units at their petroleum refinery located in Mississippi.

Providing Cost Savings and Safety Improvements to an Aircraft Manufacturer
The company involved in this case study manufactures small military and jet driven aircraft, as well as tires, TFS customer for many years.
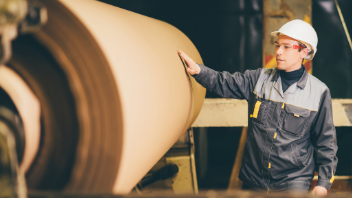
Forging a Strategic Partnership With a Global Leader in Renewable Resources
A global fiber-based product industry leader specializing in sustainable packaging and absorbent pulp solutions was searching for a strategic partnership focused on reducing their total cost of ownership and streamlining their sourcing process. Download the case study to learn why they chose TFS.
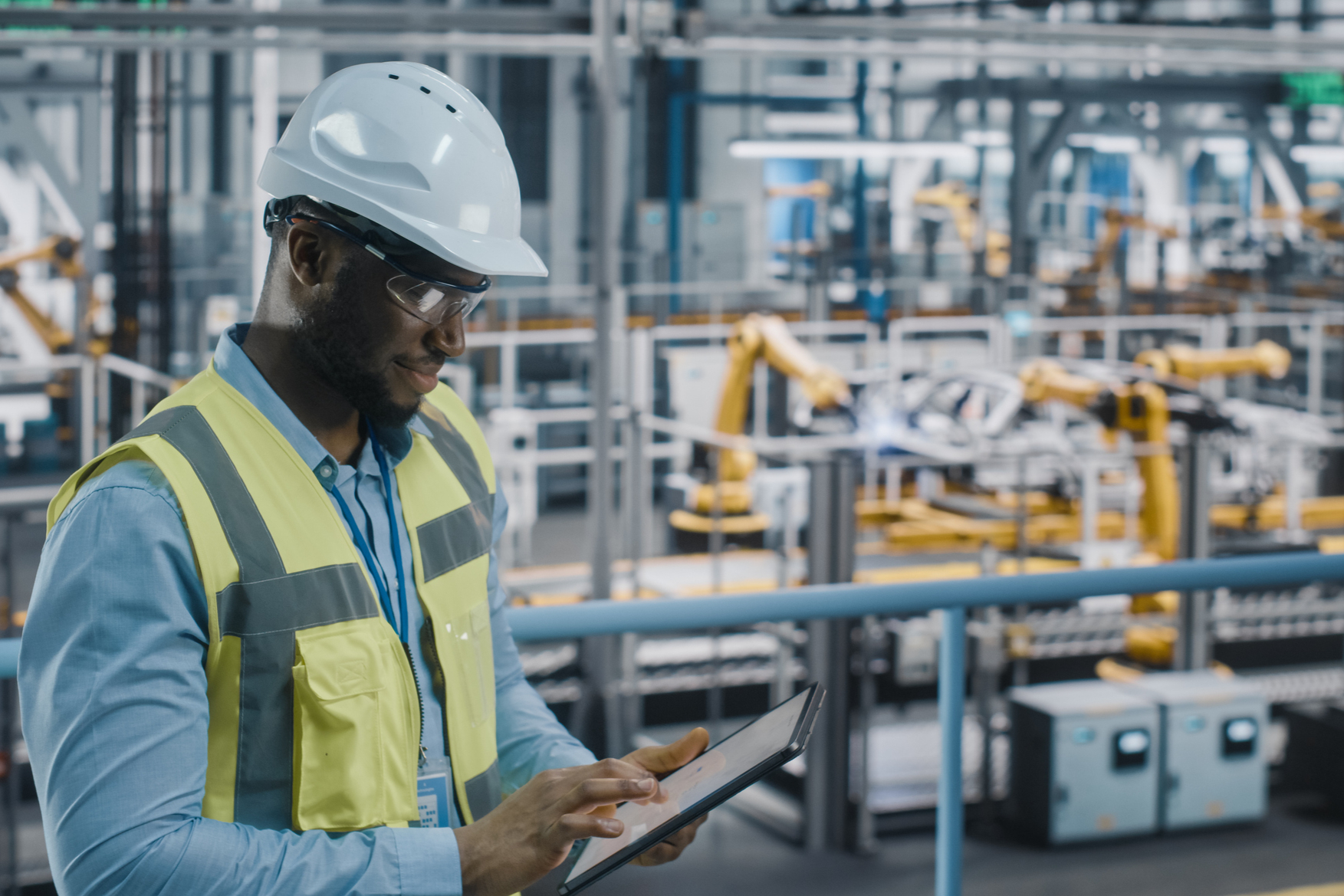
How a Strategic Filtration Overhaul Saved an Automobile Plant $3.5 Million
A multinational automobile manufacturer partnered with TFS to help with solving inefficiencies and reducing costs associated with their new hook washing system at their axle assembly plant.
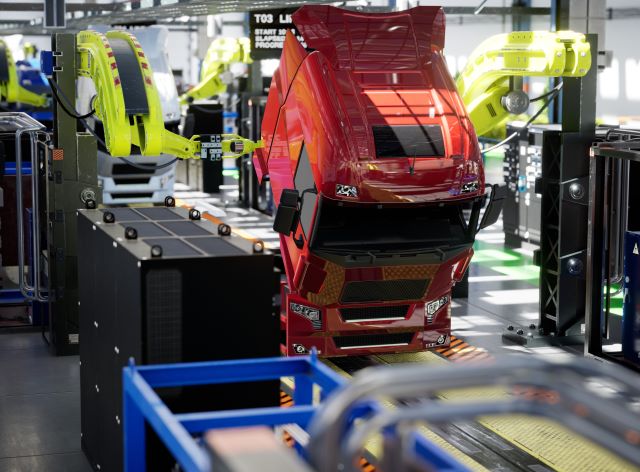
How the BowTie Filter Boosted Efficiency for a Truck Industry Leader
A large truck manufacturer needed to address safety and production downtime concerns for their paint spray booth. Read the full case study to uncover the impact of the Bow Tie filter solution on their operations.
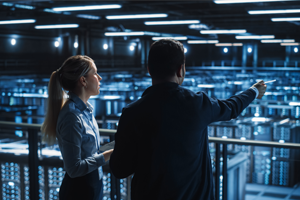
Increasing Efficiency and Preventing Downtime for Data Centers
An American company specializing in building data centers contacted TFS to address collapsing filters in their evaporative cooling units. Learn how TFS resolved the issue, improved energy efficiency, and reduced labor and waste disposal costs.
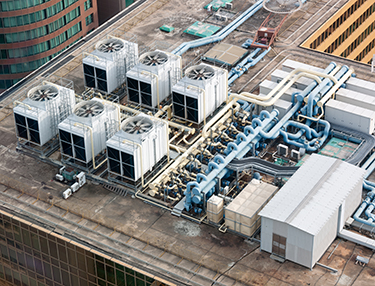
Lowering the Total Cost of Ownership for Commercial Buildings
The customer involved in this case study manages a three-building office park totaling over 416,000 square feet of office space and was looking for ways to reduce their maintenance and disposal expenses. The TFS solution resulted in a reduction of their total cost of ownership by nearly $36,000 in the first year, as well as a reduction of CO2 emissions by nearly 130,000 pounds.
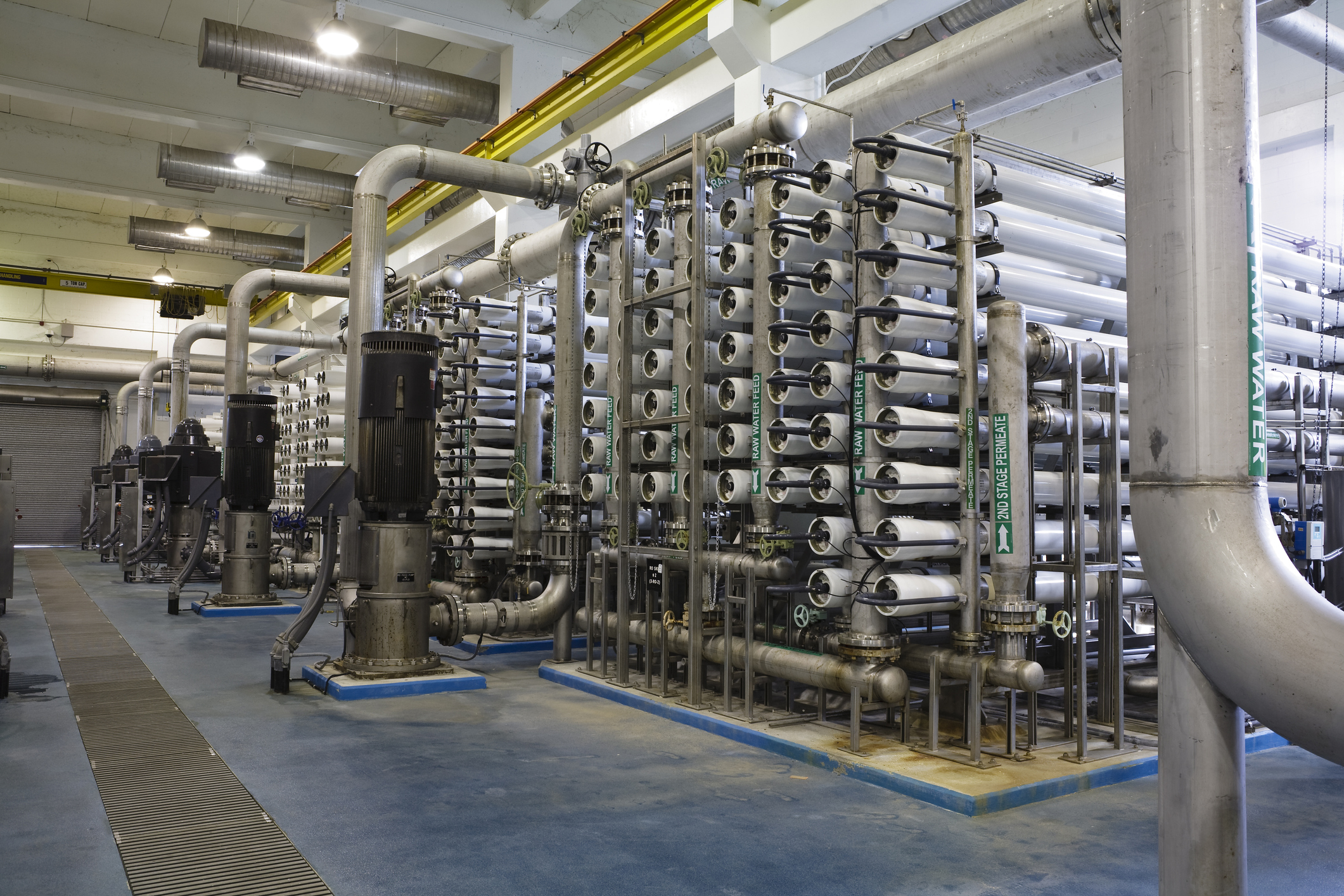
Rapid Response Prevents Process Disruption for Major Agricultural Processor
A large food ingredient facility in the Midwest experienced an unexpected disruption in their process that caused them to exhaust liquid filter cartridges faster than expected. Total Filtration Services responded immediately, coordinating after-hours efforts to deliver nearly 3,000 filters the same day—helping the customer maintain operations and avoid a costly shutdown.
Contact a Dedicated TFS Representative
TFS has developed an extensive product offering through partnerships with industry leading manufacturers. Count on us to meet your needs while improving your facility’s operation and efficiency.